Comprehensive Guide: What is Porosity in Welding and How to Prevent It
Comprehensive Guide: What is Porosity in Welding and How to Prevent It
Blog Article
Porosity in Welding: Identifying Common Issues and Implementing Ideal Practices for Avoidance
Porosity in welding is a pervasive issue that typically goes undetected till it creates substantial problems with the integrity of welds. In this discussion, we will check out the essential aspects contributing to porosity development, examine its harmful impacts on weld performance, and talk about the finest methods that can be embraced to reduce porosity incident in welding processes.
Common Reasons For Porosity

Another regular culprit behind porosity is the existence of contaminants externally of the base steel, such as oil, grease, or rust. When these impurities are not efficiently gotten rid of before welding, they can vaporize and end up being entraped in the weld, triggering flaws. Additionally, making use of dirty or wet filler products can present impurities into the weld, contributing to porosity issues. To minimize these common root causes of porosity, detailed cleaning of base metals, proper protecting gas choice, and adherence to optimum welding criteria are important methods in accomplishing high-grade, porosity-free welds.
Influence of Porosity on Weld Top Quality

The visibility of porosity in welding can dramatically endanger the architectural stability and mechanical residential properties of bonded joints. Porosity produces voids within the weld steel, deteriorating its general strength and load-bearing capacity. These gaps function as tension concentration factors, making the weld a lot more vulnerable to cracking and failing under applied lots. In addition, porosity can decrease the weld's resistance to corrosion and various other environmental variables, additionally decreasing its long life and efficiency.
Among the main effects of porosity is a decrease in the weld's ductility and sturdiness. Welds with high porosity levels often tend to exhibit lower influence stamina and decreased capacity to deform plastically prior to fracturing. This can be specifically concerning in applications where the bonded Check This Out parts are subjected to vibrant or cyclic loading problems. Porosity can hinder the weld's capability to properly transmit forces, leading to premature weld failure and prospective safety and security threats in crucial structures. What is Porosity.
Ideal Practices for Porosity Avoidance
To enhance the architectural honesty and quality of bonded joints, what details steps can be carried out to minimize the incident of porosity throughout the welding procedure? Using the appropriate welding method for the details material being welded, such as changing the welding angle and weapon placement, can further avoid porosity. Routine examination of welds and immediate remediation of any type of problems determined throughout the welding procedure are essential practices to avoid porosity and create high-grade welds.
Importance of Proper Welding Techniques
Executing appropriate welding methods is vital YOURURL.com in making certain the architectural honesty and top quality of bonded joints, constructing upon the structure of efficient porosity avoidance procedures. Welding methods directly impact the overall strength and resilience of why not try these out the welded framework. One vital facet of appropriate welding methods is preserving the appropriate heat input. Too much warmth can cause boosted porosity due to the entrapment of gases in the weld pool. Conversely, not enough warm may result in insufficient combination, creating potential powerlessness in the joint. Furthermore, utilizing the appropriate welding criteria, such as voltage, present, and travel rate, is important for achieving audio welds with very little porosity.
Moreover, the choice of welding process, whether it be MIG, TIG, or stick welding, need to line up with the details requirements of the job to make certain optimal outcomes. Correct cleaning and preparation of the base steel, as well as choosing the ideal filler product, are also necessary parts of competent welding methods. By sticking to these best practices, welders can lessen the threat of porosity formation and produce top quality, structurally audio welds.
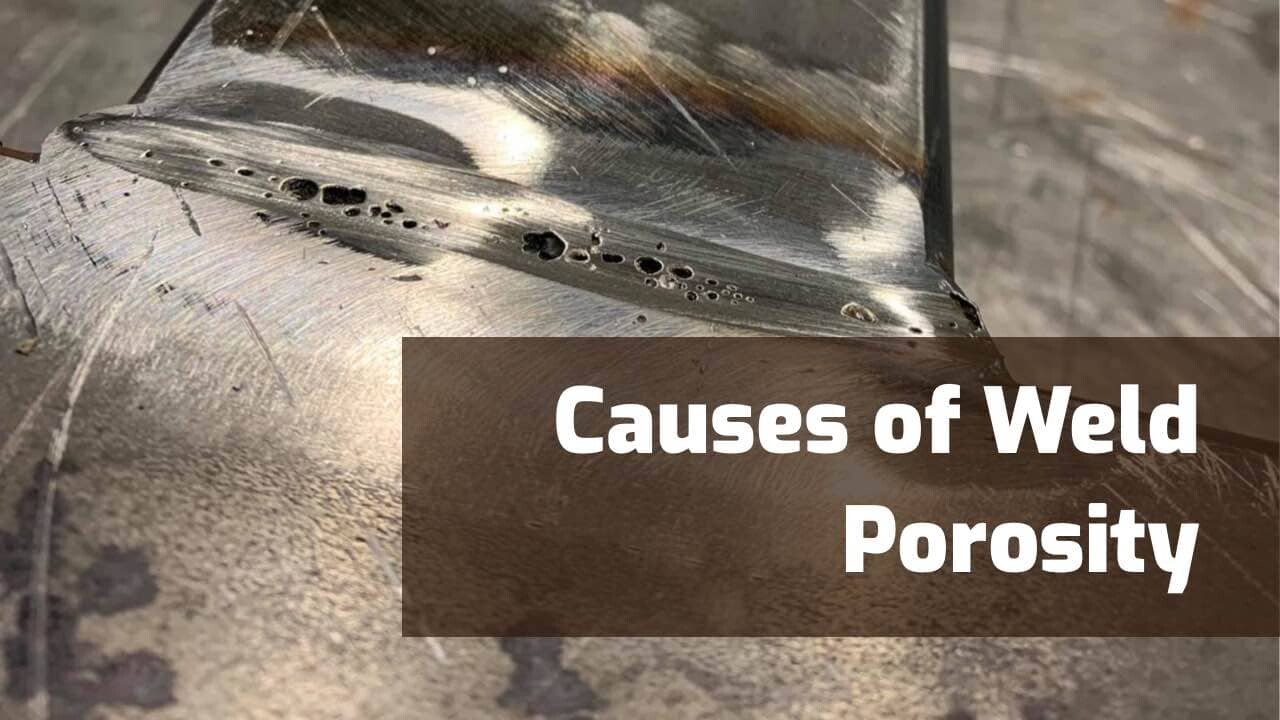
Testing and Quality Assurance Steps
Quality control procedures play an essential role in verifying the integrity and reliability of welded joints. Evaluating procedures are vital to discover and stop porosity in welding, making sure the stamina and toughness of the last item. Non-destructive testing methods such as ultrasonic testing, radiographic screening, and aesthetic inspection are frequently used to recognize prospective flaws like porosity. These methods permit the assessment of weld top quality without endangering the stability of the joint. What is Porosity.
Carrying out pre-weld and post-weld inspections is likewise critical in preserving quality assurance standards. Pre-weld assessments entail verifying the products, tools settings, and tidiness of the job location to avoid contamination. Post-weld assessments, on the various other hand, assess the final weld for any type of issues, including porosity, and verify that it satisfies defined criteria. Implementing an extensive quality assurance strategy that consists of comprehensive testing treatments and examinations is extremely important to reducing porosity issues and guaranteeing the general top quality of bonded joints.
Verdict
In final thought, porosity in welding can be a typical issue that impacts the top quality of welds. By recognizing the typical root causes of porosity and implementing ideal methods for prevention, such as correct welding strategies and testing measures, welders can make certain high top quality and reputable welds. It is necessary to prioritize avoidance techniques to reduce the incident of porosity and keep the integrity of bonded frameworks.
Report this page